
Key chemicals industry trends in 2025
How leading organizations are prioritizing the design and production of chemicals and materials that are better for our health, the environment and the economy.
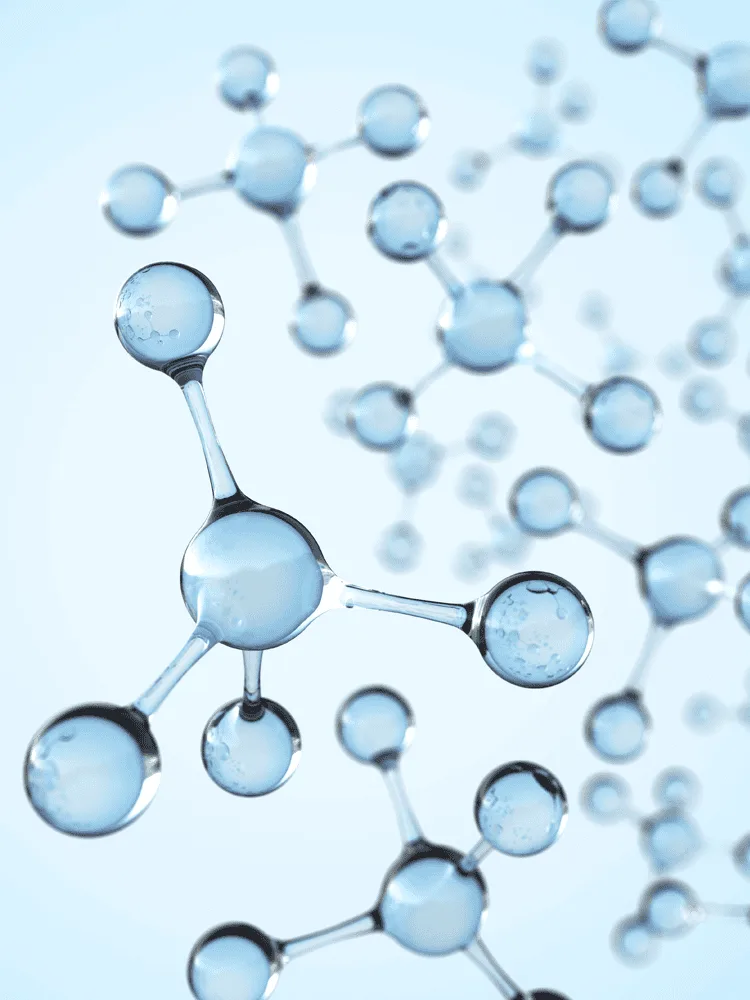
Research indicates that innovators and green leaders in the chemicals industry are best placed to maintain competitive differentiation and value creation. In an analysis by McKinsey se abre en una nueva pestaña/ventana, chemical companies with greener product portfolios yielded higher total shareholder returns than companies with less sustainable product portfolios.
The urgency of reducing carbon emissions is driving rapid innovation in the chemicals industry, along with the need to maintain business viability amid economic and geopolitical unpredictability. These are four areas where chemicals and materials organizations are focusing in order to drive sustainability and continued growth.
Bio-based materials and feedstocks
Bio-based materials are substances derived from living organisms, such as plants, animals, and microorganisms, rather than from fossil fuels or synthetic chemicals. These materials are renewable, biodegradable, and often have a lower environmental impact compared to traditional materials. Examples include bioplastics made from corn starch, natural fibers like cotton and hemp, and bio-based composites used in construction and packaging.
Bio-based materials, such as bioplastics, have become an area of significant interest in discussions around the future of materials. se abre en una nueva pestaña/ventana Demand is growing, and major organizations are using these materials to develop sustainable food packaging, more eco-friendly cosmetics, bio-based energy sources and more.
Food packaging is one area where these materials have seen real traction, despite challenges to widespread adoption. Materials such as polysaccharides, proteins and polyhydroxyalkanoates se abre en una nueva pestaña/ventana can be obtained from biomass and used in food packaging applications.
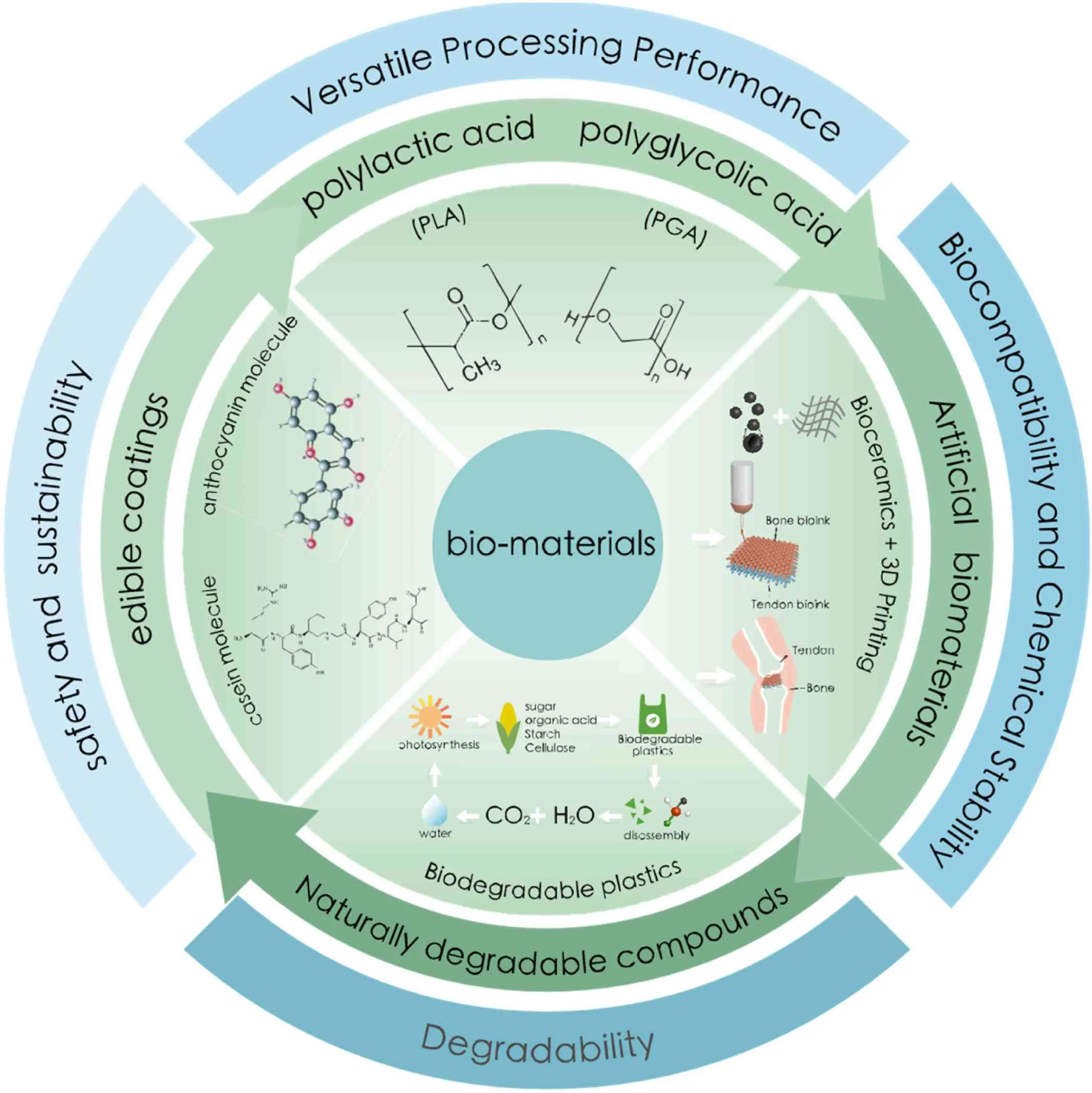
Schematic representation of the various types and properties of biomaterials. (Source: Chemical Engineering Journal Advances se abre en una nueva pestaña/ventana)
In the world of sustainable feedstocks, photosynthetic organisms like microalgae se abre en una nueva pestaña/ventanaand cyanobacteria are seen as carbon-neutral, sustainable feedstocks as their cultivation does not require arable land, pesticides and agricultural machinery. Brown algae se abre en una nueva pestaña/ventana, for instance, has a dry weight composed of 40% alginates, which can be blended with starches to create bioplastics. These organisms' photosynthetic machinery also makes them an ideal source of biomass feedstocks for biofuel. Additionally, cyanobacterial strains have been used for producing ethanol se abre en una nueva pestaña/ventana, isobutanol se abre en una nueva pestaña/ventana(a potential gasoline substitute), ethylene se abre en una nueva pestaña/ventana and isoprene se abre en una nueva pestaña/ventana.
As expected, bio-based materials face issues with scalability, as they require a significant overhaul of processes – these inefficiencies can negatively impact sustainability initiatives along the way. In addition, applications such as food packaging are still limited due to the poor performance of these materials in extreme conditions. The continued development of a robust bioeconomy se abre en una nueva pestaña/ventana is essential to the success of bio-based materials initiatives.
Safe and sustainable-by-design (SSbD) chemicals
In 2020, the European Commission published a chemicals strategy for sustainability se abre en una nueva pestaña/ventana that introduced the concept of safe- and sustainable-by-design (SSbD). It defined SSbD as se abre en una nueva pestaña/ventana “a pre-market approach to chemicals that focuses on providing a function (or service), while avoiding volumes and chemical properties that may be harmful to human health or the environment, in particular groups of chemicals likely to be (eco) toxic, persistent, bio-accumulative or mobile.”
This approach requires a lifecycle perspective and urges chemical producers to assess the environmental and human impacts of every stage of chemical development and usage.
While the SSbD framework is still a work in progress, the European Commission’s Joint Research Centre has recommended a two-phase approach for developing SSbD criteria. The first step focuses on four design principles:
Green chemistry — e.g., using waste as sustainable feedstock
Green engineering — e.g., self-healing designs, such as concrete with bacteria se abre en una nueva pestaña/ventanathat automatically fills in cracks
Sustainable chemistry — e.g., redesigning processes to create better products, such as genetically engineering microalgae to become a more efficient feedstock
Circularity by design — e.g., compostable food packaging that can be re-incorporated into the production cycle multiple times
The second step is an assessment of material and chemical hazards, human health and safety effects in the processing phase, human health and environmental impact in the use phase, lifecycle, and social and economic sustainability.
These steps align with the view of Cefic, the European Chemical Industry Council, which says any SSbD criteria must address environmental, social and economic factors se abre en una nueva pestaña/ventanaand take a lifecycle approach.
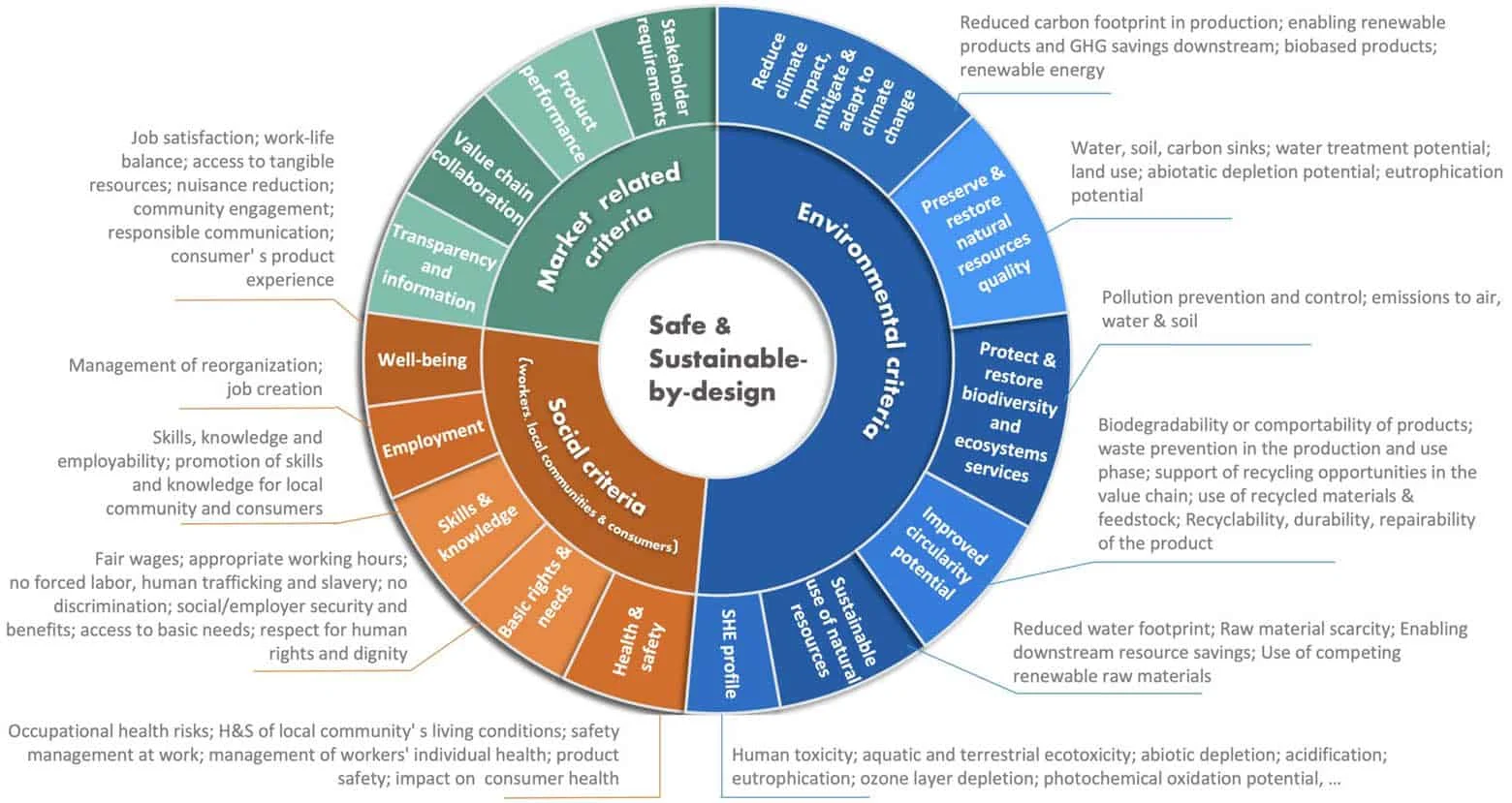
Cefic’s map of SSbD criteria from the chemicals industry (Source: cefic.org se abre en una nueva pestaña/ventana)
Adopt SSbD across your product portfolio by identifying chemicals and processes that can be substituted with alternatives that are safer, emit fewer greenhouse gasses, and allow for easier composting and upcycling.
AI in chemicals R&D
Due to its ability to speed up R&D and cut prediction inaccuracy by about 50% se abre en una nueva pestaña/ventana, AI is now seen as a way to boost profit, productivity and sustainability in the chemical industry. Machine learning and predictive analytics can augment R&D efforts, such as by identifying optimal synthetic routes for novel compounds, predicting unwanted properties, and forecasting material costs.
The energy and chemicals industries remain slower to adopt AI se abre en una nueva pestaña/ventana than other areas, which presents opportunities for organizations that wish to be on the leading edge. Chemicals R&D relies on access to relevant scientific data and market intelligence, and AI can bring significant time savings to these processes and fuel faster, more-confident decision-making.
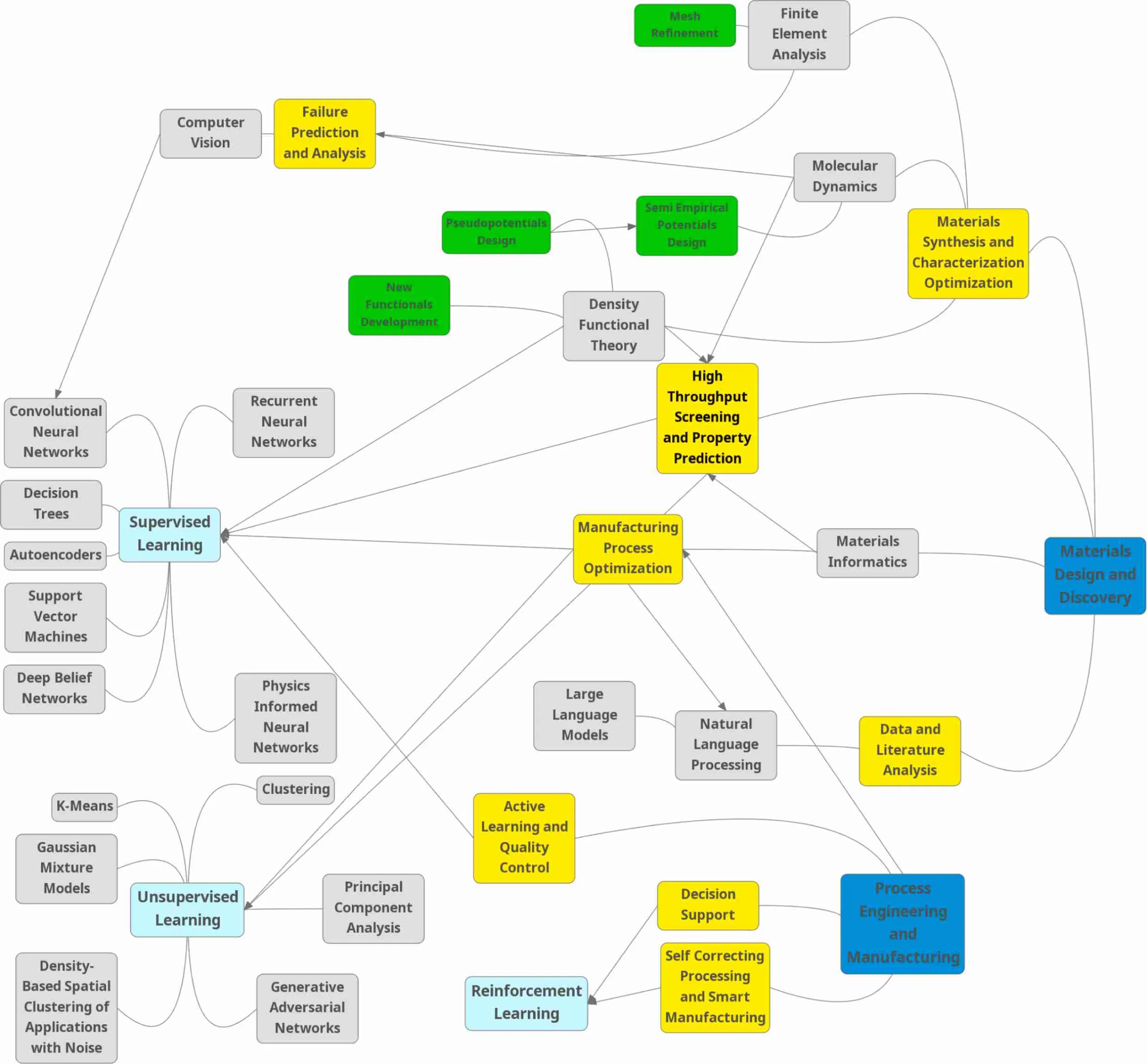
Conceptual overview of AI/ML methods in Materials Science (Source: Computational Materials Science se abre en una nueva pestaña/ventana)
Materials discovery is one area where the potential of AI is significant. Using techniques such as machine learning, companies can quickly pull information from patents, proprietary data, published journals, scientific literature, public databases and industry bodies. Machine learning can also monitor innovation from other companies in the market for a competitive advantage.
In addition, using neural networks and knowledge graphs, chemicals and materials companies can:
Predict properties of new materials
Optimize existing materials or find new applications for existing materials (repurposing)
Identify new catalysts for chemical reactions
Reduce the number of iterations needed to design a new material or compound
Click here to download our ebook on AI and the materials development race.
Specialty chemicals
Chemical companies in 2025 face continued economic challenges se abre en una nueva pestaña/ventana, though many began to see a significant bounce back in 2024. Many leaders continue to invest in decarbonization and innovation while looking to cut costs and increase their margins. High-demand, high-margin products like specialty chemicals are one such solution.
Specialty chemicals, also known as performance chemicals, are based either on single molecules or on formulations of mixed molecules. Specialty chemicals heavily influence the way a product functions.
Globally, the most in-demand specialty chemicals are electronic chemicals, specialty polymers, industrial and institutional cleaners, surfactants, and flavors and fragrances, according to S&P Global se abre en una nueva pestaña/ventana. Demand will continue to rise, with the market size for specialty chemicals se abre en una nueva pestaña/ventanaexpected to grow from $641.5 billion in 2023 to $914.4 billion in 2030. Much of this demand will come from the need for construction, electronics, pharmaceutical and water treatment chemicals.
There is also an increasing demand in electronics and consumer goods for safe and sustainable specialty chemicals. For example, Apple has set its own regulations on specialty chemicals, which need to be followed in the production of its products. The Apple Regulated Substances Specification se abre en una nueva pestaña/ventanais publicly available and outlines how the company aims to remove harmful substances from the product life cycle.
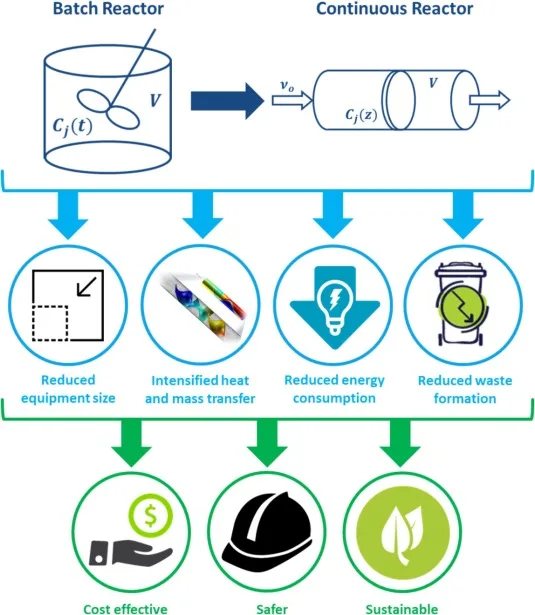
Batch-to-continuous transition offers strong improvements to the production process. (Source: Chemical Engineering Journal, Volume 445 se abre en una nueva pestaña/ventana.)
To improve profits in this highly competitive segment and become more valuable to your customers, invest in downstream opportunities se abre en una nueva pestaña/ventana like providing support services to clients and developing customized and novel formulations. This shift toward a more service-oriented approach also raises the entry barriers for competitors as it requires specialization and ongoing collaboration with clients.
Upcoming sustainability webinar from Elsevier
As the chemicals industry transitions toward a low-carbon future, R&D organizations must adapt to evolving market demands, regulatory pressures, and technological advancements. To stay ahead, companies need strategic talent, skills and capabilities to drive innovation in sustainable energy, industrial processes and transportation.
We invite you to the first session of our 2025 webinar series, where Dr. David Hatrick, Vice President of Strategic Marketing and Innovation at Huntsman Advanced Materials, will discuss how organizations can navigate these challenges and position themselves at the forefront of sustainability.
Join us on March 18, 2025, by registering for free at this link. se abre en una nueva pestaña/ventana We look forward to seeing you there!
Join us on March 18 for the latest on sustainability in action.
Sign up for the Industry Sustainability Insights newsletter
Sign up for a quarterly email update from Elsevier on the latest Industry Sustainability Insights, which spotlights hot industry topics, information on upcoming webinars, new articles and other resources.
Learn more about sustainable innovation with Elsevier
Read more insights into chemical industry innovation and learn more about how Elsevier supports the world's leading engineering organizations.